Popular Science Monthly/Volume 18/January 1881/Domestic Motors II
DOMESTIC MOTORS. |
By CHARLES M. LUNGREN.
II.—STEAM AND HOT-AIR ENGINES.
SMALL steam-engines of from two to ten horse-power are made by a number of engine-builders, and are quite extensively used. They are of varied excellence, like those of larger size, and are well enough known to need no description here. Those of powers of one horse and under suitable for use in the household, for amateurs, etc., are, however, comparatively rare. The danger of explosion, and the requirement of skilled attendants, which in cities the law in consequence imposes, have operated to prevent their use; while, on account of the but little greater cost of the larger and more serviceable machines, makers have preferred to construct the latter. Some of these small engines are, however, made, two of the best designs of which, the invention of Mr. H. S. Maxim, are shown in Figs. 4 and 5. The one illustrated in the first engraving is constructed for pumping purposes only, and that in Fig. 5 for power. Both forms use gas in the smaller sizes, and are entirely automatic in their action. They are compact, highly finished,
Fig. 4.

and can be used anywhere in a house without annoyance, as they run with almost no noise. They occupy but small space, the boiler-casing being in the smallest size but sixteen inches in diameter and three feet in height. The base of the machine has air-spaces to prevent the heat from burning the floor. The construction and operation of the pumping-engine will be clear from an inspection of the cut. The heater B surrounds the boiler C C, which is made with pendent water-tubes G G, among which the burning gases circulate on their way to the smokestack. The gas burns from a double argand burner H, the supply being automatically controlled by the steam-pressure in an ingenious manner. At I, a valve is placed in the gas-pipe which is operated by the lever l, the longer end of which is pressed up by the spring M. A tube, o, leads from the boiler to a chamber in which works the diaphragm-piston r, attached to the shorter end of the lever L. If the pressure in the boiler increases, it is transmitted to the piston which rises and partially closes the valve I, diminishing the supply of gas. A lessening of the boiler-pressure produces the reverse effect of increasing the gas-supply. The amount of fuel consumed is thus accurately proportioned to the amount of steam generated by the engine itself. This allows the gas to be kept burning while no work is being done, and consequently no steam used without there being the slightest danger of an explosion, a feature of great value in a power-engine when it is used intermittently, but needs to be in constant readiness. In the larger sizes in which coal is used, the fire is regulated by means of an automatic damper operated in a similar manner to the valve controlling the gas-supply.
The feeding of water to the boiler is also controlled by a very simple automatic arrangement. The feed-water chamber is placed at the top of the heater-shell, where it is exposed to the heat of the issuing products of combustion. A pipe, h, is open to both the pump and this chamber. So long as the feed-water heater is but partially filled, water continues to be forced into it by the pump; but, when it becomes full, no more can enter until a portion of it has passed into the boiler. The admittance to this latter is controlled by a float mechanism, E, F, D, operating a valve at the base of the boiler through the medium of the rod o. The float E is a flat, inverted vessel, which is partially submerged when the boiler is full. A weight, D, at the other extremity of the lever F, is then able to keep the valve closed; but, as the level of the water sinks, the float drops and the valve is opened by the rod o, the pressure produced by the pump forcing water from the feed heater into the boiler. By these two devices, the one controlling the heat by the steam-pressure so as to keep that pressure constant, and the other regulating the amount of water in the boiler, this steam engine becomes nearly as safe, and gives as little trouble, as any of the simpler forms of heat-engine using hot air or gas. For still further security a safety-valve is placed in the pipe leading from the boiler, at A; and in the engines using coal, the heat of which can not be so perfectly controlled as that of gas, a plug of fusible metal is set into the crown-sheet, which melts when the temperature rises above a certain point, and allows the water to flow out and extinguish the fire.
Fig. 5.

The design of the boiler of the power-engine is somewhat different from that of the pumping one, but the means of automatically regulating both the steam-pressure and the water-supply are substantially the same. This engine has in addition a very ingenious governor which acts directly upon the point of cut-off as in the best machines of large power. It is placed inside the belt-pulley, and dispenses with the ordinary belt, thereby avoiding the danger of the engine racing through the breaking or slipping of the belt. The balls are two heavy weights revolving with the belt-pulley, and balanced by spiral springs. They are free to move in the direction of the radius of the wheel to and from the center, and, as they do so under variations of speed, they operate the cut-off mechanism in a simple manner. The working of this governor has been found very satisfactory in use, and it seems to be well suited to engines of larger power. This engine is made in sizes of one half, one, one and a half, two, and two and a half horse-power, and up to five horse, while the pumping-engine is made of a capacity of from two hundred and fifty to fifteen hundred gallons per hour, raised one hundred feet high. The former amount is pumped with an expenditure of twenty-five feet of gas an hour. These engines have been on the market some five years, and have been found very satisfactory in use.
An engine of very much smaller power, and quite novel construction, the invention of Mr. Charles Tyson, has very recently been brought out, which seems to be well adapted to driving such light machinery as sewing and knitting machines, lathes, scroll-saws, fans, coffee-mills, etc. It is quite safe, requires but little care, does not easily get out of order, and can be managed by any one capable of using a sewing-machine. It is ornamental in design and handsomely finished, fitting it to be used in any room of a dwelling that is convenient. Those at present made are of about one quarter of a man-power (one thousand foot-pounds per minute), but larger sizes, adapted to a greater range of
Fig. 6.
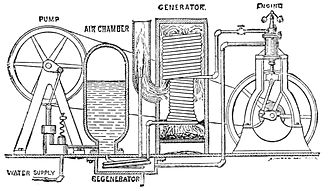
work, will probably be built should the present machine prove satisfactory in use. Gas is used as fuel, but they can be made to burn either coal, wood, or oil. The construction and method of generating steam are such that an explosion can not occur, and the steam-gauge, water-gauge, and safety-valve are therefore dispensed with, with the advantage of considerably lessening the cost. The idea carried out in the construction of this engine is that of converting the water into steam in small amounts at a time. In the steam-engine, large or small, the whole body of water is exposed to the action of the fire, and a considerable quantity of steam is constantly generated. In this, small quantities of water are successively forced from a reservoir through coils of highly heated tubing, and there flashed into steam. A force-pump driven by the engine continually supplies water to the reservoir. The relation of the different parts of the apparatus to each other, and the working of the system, are clearly shown in Fig. 6. The long tubing, in which the water is converted into steam, leads from the air-chamber to the steam-chest of the engine. It is coiled first in a receptacle through which the exhaust steam passes, and then in the generator, where it is as completely as possible exposed to the action of the fire. In starting the engine, the fly-wheel is turned by hand, so as to produce a pressure in
Fig. 7.

the air-chamber. This forces the water into the coil, where it is rapidly converted into steam, and delivered in the steam-chest at the pressure furnished by the pump. When the engine begins running, it drives the pump and maintains the pressure. If the engine is stopped and the fire continues to burn, the water in the coil will be forced back into the air-chamber, and the production of steam will cease.
When the water is exhausted, the engine simply stops until the supply is renewed. At the right of the pump a relief-valve is placed to limit the pressure. It is not a safety-valve, as, even if it were absent, an explosion could not occur, as the mechanism of the pump is not strong enough to produce a bursting pressure. The construction of the generator is more fully shown in Fig. 7. It consists of a cylindrical shell in which is coiled about thirty-five feet of seamless copper tubing. In the base of this is a gas-burner, L, and around it is a second shell, leaving an annular space for the entrance of air. The air is also admitted through openings at the bottom of the shell. The burning Fig. 8. gases pass up through the center of the coils and down between the two, and out by the draught-pipe. The exhaust steam is discharged through the regenerator, where it partly heats the water in the coil, into this draught-pipe. On first lighting the gas, the cap A’ is removed and the flame allowed to burn up into the air, but as soon as the formation of steam begins the cap is replaced, and the exhaust steam then creates sufficient draught to carry the burning gases through the coils into the draught-pipe. The generator has but one fiftieth the cubical capacity of that required by an ordinary boiler to run the same engine. The engine is of the simple oscillating type, and the whole apparatus is attached to a bed-plate forming the top of a vase-shaped receptacle. Fig. 8 shows the appearance of the complete motor. In another form the vase is supported by a bracket attached to the wall instead of by the tripod. The vase is used to hold the water from which the pump supplies the reservoir. Four or five quarts of water once in as many hours is generally sufficient in the ordinary use of the machine.
The engine in this size is far from being economical, requiring twelve cubic feet of gas an hour, while it only furnishes a thirty-third of a horse-power. Efficiency, however, is not very important with such a small motor. This amount of fuel, with gas at two dollars per thousand, would only cost a little more than two cents an hour, which would make the expense of running a sewing-machine as commonly used inconsiderable. The first cost of the motor is low, while its simplicity of construction should render it quite durable.
The advantages possessed by engines driven by heated air over those using steam, in the matter of safety, absence of the need of skilled attendance, and a possible higher efficiency, early turned the attention of inventors toward the development of this class of motors. Promising as the field seemed, the practical realization of the hopes indulged in has been far short of expectation. The rapid alternate heating and cooling of the air, and the prevention of excessive wear due to traveling surfaces becoming highly heated, have been found to be difficult things to accomplish satisfactorily. On account of the low pressure obtained from heated air, engines of this kind have to be made of such large dimensions that there is little if any gain in compactness over the steam-engine and boiler. This greater size of the working parts also increases friction largely, so much indeed that whatever superior efficiency the hot-air engine may possess, from being able to work between greater extremes of temperature, disappears in the power required to move simply the machine itself. In large powers this engine has never yet been able to compete with the steam-engine, but in small ones it has proved to be quite an economical and serviceable motor. A number of engines of this kind have been invented at different times, and some have gone more or less largely into use. The earliest to excite interest, and to come into a limited use, was that of Rev. Dr. Stirling, in 1816, which was successively improved by him and his brother up to 1840. Among the engines which have been more or less successful have been those of Ericsson, Wilcox, Roper, Shaw, and Rider in this country, and Lauberau and Belou in France. Hot-air engines are broadly divided into two classes by the manner in which they use the air. In one class it is drawn directly from the atmosphere, used, and then discharged. In the other the same body of air is used continuously, being alternately heated and cooled. The latter class has the advantage of being able to use the air at a greater pressure, but they need a refrigerating apparatus, which is unnecessary with the first. When the engine is used for pumping purposes this constitutes no disadvantage, as the water can be passed around the part of the cylinder desired to be kept cool, and even when it is used as a motor, a water circulation can very readily be kept up by means of a supply tank of sufficient capacity. As the efficiency of any heat engine depends upon the extremes of temperature between which it is worked, either the air used in the air-engine should leave the power cylinder at the temperature of the atmosphere, or it must be made to give up a portion of its heat to some apparatus that will yield it again to the entering air. The first is impracticable, and attention has therefore been given to the construction of such an apparatus, termed a regenerator. This has taken various forms in different machines—from a number of simple perforated plates to nests of tubes. Practically it has been found most economical to attempt to abstract only a part of the heat, as to do more offers too great an obstruction to the passage of the air, with the result of losing as much in power as is gained in heat.
One of the earliest hot-air engines to obtain a recognized place as a valuable aid to motive power was the well-known engine of Ericsson, which has long been on the market, and has come into somewhat general use. It is of the class using a fresh charge of air with each stroke, the air being drawn into the cylinder, compressed, heated, and, after doing its work, discharged. The engine is made both for pumping and power, and is constructed in sizes up to four-horse. It is too well known to require any description here.
Fig. 9.

Quite recently a new and much simpler engine designed for pumping purposes has been perfected by Mr. Ericsson, and is now being manufactured. It belongs to the class in which the same air is used over and over again, being alternately heated and cooled. The cylinder is placed upright, and projects below a table, by which it is supported, into the fire-box placed beneath. This is an iron shell provided with the ordinary grate and brick-lining at its lower end when the fuel used is coal, and with three Bunsen burners when it is gas. The latter fuel is much the most desirable, as it is cleanly, no trouble, and allows of starting and stopping quickly, and of always having the heat under perfect control. The working parts of the engine are a piston fitting the cylinder tightly, a plunger moving in it loosely, and the system of cranks and connecting-rods by which the motion of these parts is communicated. The upper portion of the cylinder, through which the tightly fitting piston alone moves, is water-jacketed, and consequently remains cool, while the part below this becomes more or less highly heated. In this heated portion the plunger moves, alternately displacing the air from above the fire. It is a long iron shell filled with wool or other non-conductor, and provided with studs on its sides which keep it from the walls of the cylinder. The machine is started by giving a few turns to the fly-wheel, when it begins running of itself, the action being as follows:
The plunger being raised, the air below it is heated and expands, forcing the piston upward. As it does this, the plunger is brought down with a quick motion, displacing the air, which passes through the annular space between the plunger and cylinder wall to the upper part of the cylinder. Here it comes in contact with the cool surface of the water-jacketed portion and contracts, forming a partial vacuum below the piston, which then descends by atmospheric pressure. By the upward movement of the plunger, the air is again brought in contact with the heated bottom and sides of the cylinder, and the same operation is repeated. The plunger-rod passes up through the piston, and by means of the simple system of connecting-rods and cranks shown in the figure the proper motion is given the plunger. The pump is placed at the side of the cylinder, and its rod connected directly to the beam of the engine. The water is drawn into the pump and discharged through the water-jacket, the slight heating of the water in its passage through the jacket being no disadvantage, while the continual passage of fresh water readily keeps the cylinder cool. The engines have so far only been made for pumping purposes, but they can readily be adapted to those of a small power, by using only a part of the power of the engine in pumping. Four sizes of the motor are made, three with single cylinders, six, eight, and twelve inches in diameter, and one with two cylinders of the latter size. The first lifts two hundred gallons of water fifty feet per hour, with an expenditure of fifteen feet of gas, the second three hundred and fifty, the third eight, and the fourth sixteen hundred gallons, the same height, with a proportional consumption of fuel. The prices vary from two hundred and ten dollars for the smaller to five hundred and fifty dollars for the largest size. Only the two smaller sizes are at present made to burn gas. They are perfectly safe, so simple that they can be used by the most inexperienced persons, and for their special purpose are probably as cheap and satisfactory machines as can be made.
Another engine, and one of the most serviceable of this-class of machines to be found in the market, is the Rider compression engine. Like the other hot-air engines, it is constructed chiefly with a view to pumping, but when desired for power in addition it may be obtained fitted with a governor and the necessary pulleys at a slight increase of cost. The pumping-engines have found their way into very general use on railroads, country seats, and in city buildings, and from their economy in the use of fuel and their little trouble they have in all these situations proved very satisfactory. They are made only with coal-burning furnaces, and are on this account more troublesome than they would be if using gas, but are still but little more so than an ordinary coal-stove. Replenishing of fires and oiling are the only duties to be performed, and these can be done by unskilled labor. The engine occupies about the same floor-space as a moderately large coal-stove, and is about the same height. Two sizes are made, one of six, and one of ten-inch cylinder. The former will pump five thousand gallons of water to a height of ten feet in an hour, or a smaller amount to a proportionally greater height, at an expenditure of four pounds of coal, and the latter will raise twelve thousand gallons to the same height, in the same time, with eight pounds of coal. These amounts of coal are those used when the engine is run consecutively for ten hours. If run for a shorter time, the coal consumed per hour will be somewhat greater, owing to the starting of the fire. The engines weigh considerable, the smaller size being some sixteen hundred pounds, and the larger about double. The prices do not differ materially from those of steam-engines of from one to three horse-power.
The internal construction of the engine and manner of working; are shown in the sectional view in Fig. 10. It is also of the type which repeatedly uses a given body of air, but, unlike the motor of Ericsson, the alternate heating and cooling are done in separate cylinders. The air is heated in the cylinder B and cooled in the cylinder A. The plunger C fits the cylinder A in its upper portion, but is contracted in the lower part to allow of an annular space between it and the wall of the cylinder. The power-piston D also fits its cylinder B tightly in the upper portion, but loosely in the lower heated part. A leather packing, K K, in each cylinder secures as in other engines a perfect fit of these moving parts. Between the two cylinders is placed a regenerator, H, consisting of a number of perforated plates, through which the air passes in going from one cylinder to the other. Around the lower portion of the cylinder B is a water-jacket, E, and encircling the same part of the heating cylinder B is a metal shell, F, curved inward at the base. The extension G of the cylinder B down into this shell forms a narrow annular space, through which the air entering the heater has to pass in a thin sheet, and thus becomes thoroughly heated. In action, the plunger C descends and compresses the air below it to one third its previous bulk; then by the further upward movement of the power-piston D and the completion of the down-stroke of the plunger, this air is transferred to the heater. This compressed air becoming heated expands and forces the power-piston to the end of its stroke, and entering the cylinder A carries the plunger nearly to its extreme upper position. The air in contact with the water-jacket becoming cooled contracts, and the pressure is reduced below the power-piston, which then descends by the force of the atmosphere. As it reaches the end of its downward stroke and begins
Fig. 10.

to ascend, the plunger comes down and the operation is repeated. When the air passes from the heater to the cool cylinder A, it heats the plates of the regenerator and this heat is given off to the cool air, when it is again forced into the heater. The utmost of the heat is thus utilized that is possible. The start in this as in all hot-air and gas engines must be made by hand, but after a few turns of the fly-wheel the motion acquired is maintained by the engine.
The engine is supplied with either a deep well-pump, or one for use when the water is not more than twenty or twenty-five feet below it. The former is a simple contrivance, tubular in form, so that it can readily be inserted in artesian wells. The pump for use with water at less depths is of special construction, provided with rolling valves. It is bolted to the cooling cylinder, and worked directly from the compression piston or plunger. With one or the other of these pumps the motors can be adapted to every variety of circumstance in which water is to be drawn from one point and conveyed to another. Houses in the country can have as complete a water-supply, and have it in as convenient a shape, as those in the city, and at but little greater cost.
One of the best of this class of motors made for power purposes is the Sherrill-Roper engine, shown in section in Fig. 11. The manner
Fig. 11.
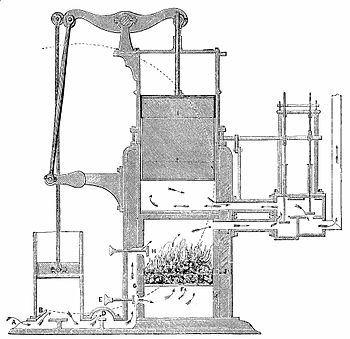